Arkansas Sharpening Stone Grits
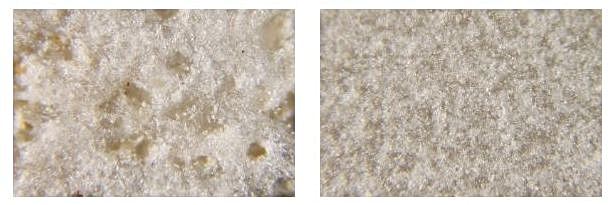
Topics Covered:
Arkansas sharpening stones are made of Novaculite. Novaculite is a rock that is comprised of quartz crystals. Quartz is hexagonal in shape and has sharp edges. These sharp edges give Arkansas stones their unique sharpening abilities. - What Grit is an Arkansas Stone?
- What is Grit?
- Evaluation of Arkansas Stone Grits
- Test Results
- Summary
- References
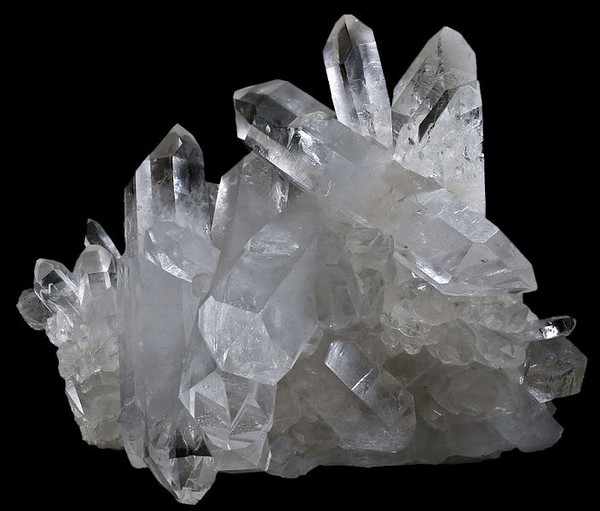
Quartz Crystal Cluster
The novaculite that Arkansas Stones are made of is composed mostly of 1-5 micron quartz grains. [1]These quartz grains are found in clusters. How densely packed together these clusters are contributes to the grit of the individual stones. Below is a recent image that shows quartz clusters from a Soft Arkansas stones that became dislodged while sharpening.
Soft Arkansas Stone Crystals
Arkansas stones also contain traces of other elements[2] such as aluminum, iron, manganese, titanium, calcium, magnesium, sodium, and potassium. These elements contribute to the color of the stones. But color does not distinguish the grits of Arkansas stones. The abrasiveness of each grade of Arkansas stone is related to the specific gravity of the stone. Specific gravity is related to the density or compactness, of the quartz crystals. The next two images illustrate this very well. On the left is a Soft Arkansas on the right is Translucent Arkansas. The difference between the densities of the two stones is clear.
Soft vs Translucent Arkansas Stones at 100x
However, specific gravity is not intended to determine the actual grit of Arkansas Stones. Specific gravity measures the density of the stone and helps in grading but it doesn't provide a grit. The best method for determining grit is evaluating scratch patterns. Using scratch patterns is a common industry practice for evaluating the grit of abrasive materials.
What is Grit?
Grit is a standard to indicate how aggressively an abrasive particle will scratch a surface. It is not actually a designation of specific particle size, but a description of an average of particle sizes. Typically a series of screens is used to sort particle sizes.
Each of these screens has a differing number of openings per inch. As abrasives are passed through one screen and retained on another we can sort them into sizes. Industry standards[3][4] allow for a wide particle size range for each of the grits. Therefore, grit is best thought of as the average particle size of an abrasive. For more information on how grits are determined please see What Does "Grit" Mean? by the 3M Company[5].
This wide range of particle size means that scratch patterns will be inconsistent, with larger particles leaving larger scratches and finer particles leaving smaller scratches. While the resulting scratch patterns may be inconsistent, using scratch patterns to evaluate grit is a common industry practice used for determining the effective grit of abrasive materials.
Microscopic Study of Arkansas Stone Grits
The purpose of this study was to determine the effective grit of the four types of Arkansas Sharpening Stones. As we discussed earlier in this article, the size of the individual quartz particles that make up Arkansas Stones are all between 1 and 5 microns. It is the density at which those particles are distributed that determines their effective grit.
Our Testing Method
We used identical blades for each test.
The Arkansas Stones we used in the test were new. Before beginning, we tested the specific gravity of each stone then broke them in by making 500 passes over an ordinary kitchen knife. We used mineral oil for a lubricant. We cleaned the stones with mineral oil before beginning the test passes.
The blades were sharpened using a Wicked Edge Sharpener. We cut the stones to size and attached them to blank Wicked Edge handles. The reason we decided to use the Wicked Edge was a matter of control. We felt we could control the pressure being applied to the blade most accurately by using the Wicked Edge.
Before we could begin testing the Arkansas stones we needed a control sample to compare them to. For our control sample we chose 3M Lapping Film because we believe it is the most carefully graded abrasive available. To get our control samples we polished 6 blades down to .3 micron.
We now had 6 polished blades with almost no visible scratches at 100x. We then sharpened 5 of the blades with 12, 9, 5, 3, and 1 micron using the lapping film. This gave us a control sample for each micron size. (We made 150 passes on each blade using Krud Kutter as a lubricant and cleaned the films every 50 passes.) We photographed the control samples at 100x magnification and put them aside.
Next, we took 4 new blades and polished them down to .3 micron. We then made 100 passes over a blade with each of the 4 types of Arkansas stones. We photographed them at 100x magnification and compared the results to the control samples we had made.
To convert the micron rating of the lapping film to grit we used two sources. We have found that when making these conversions it is best to consult with gemologists. They have been practicing lapidary[6]for at least 5000 years while the practice of using micro-abrasives for sharpening is less than 20 years old. We also used a micron to grit conversion chart from one of the oldest quality tool suppliers in North America.
The two sources we used to convert micron to grit were the Gem Cutting Abrasives In Grit, Mesh, and Microns[7] from the International Gem Society and the Grit = Micron = Mesh Conversion Chart from Gesswein[8]. Both of these charts convert microns to grits and they are easy to use.
One of the factors that made making the comparisons difficult was the variation of particle size in the Arkansas stones when compared to the man-made lapping films. Given the Arkansas stones are a natural stone the variation is to be expected but it certainly made making comparisons challenging.
You have to use an average of the scratches of both types of abrasive to make a comparison. We also looked at the apex of the various blades to help in estimating the effective grits. The below image is of the negatives of the photographs we took. It is much easier to evaluate the scratch patterns of the negatives than of the regular image.
Arkansas Stone Grit Comparisons
Arkansas Stone Grits - Test Results
Soft Arkansas - Specific Gravity 2.22 | 12 micron | .00047" | Grit Equivalent: 1200. The Soft Arkansas is close to the 12 micron lapping film but clearly finer than the 800 grit diamond stone. Hard Arkansas - Specific Gravity 2.36 | 10-11 micron | .00041" | Grit Equivalent: 1500. It is a little coarser than the 9 micron lapping film but finer than the 12 micron film.
Black Arkansas - Specific Gravity 2.55 | 7-7.5 micron | .00028' | Grit Equivalent: 2300-2500. While the Black Arkansas did have a few larger scratches, overall, it is a little finer than the 9 micron lapping film.
Translucent Arkansas - Specific Gravity 2.53 | 5.5-6 micron | .00023' | Grit Equivalent: 3500-4000. It is clearly finer than the Black Arkansas. Most closely resembles the 5 micron lapping film.
Other Observations:
1. Since the same number of passes was taken with each stone you can see the removal rate of each by the height of the edge created. As expected, the height of the edge is greatest for the Soft Arkansas. This makes sense because it is the coarsest grit. The heights of the edges get smaller for the Hard, Black and Translucent progressively. As the grits got finer, the rate at which steel was removed reduced accordingly. No surprise there but I was surprised at how much faster the Soft Arkansas removed steel compared to the other three stones.
2. We've also always heard that one of the unique sharpening properties of Arkansas Stones is that they sharpen and polish at the same time. They next two images illustrate that well. The effect is especially evident in the Black Arkansas. You can see where the coarser grains of quartz have scratched the surface deeper while the finer grains have polished. The finer scratches match closely with the 3 micron lapping film sample.
Hard and Black Arkansas Stone
Summary: The effective grit of Arkansas Sharpening Stones is finer than previously reported.
The Soft Arkansas has typically been stated at anywhere from 400 to 800 grit. The Soft Arkansas stone is close to 1200 grit.
The Hard Arkansas stone grit is slightly finer than we thought at 1500 grit. Previous estimates put it at somewhere between 800 and 1200 grit.
The test results showed us the Black Arkansas grit is 2300 to 2500 which is exactly what we expected. No surprises here.
From practical experience I have always felt the Arkansas Translucent stone is 4000 grit. There are straight razor users who have put it as high as 8000 grit. This test puts Translucent Arkansas equal to 3500-4000 grit.
The Soft Arkansas stone removed metal at a much faster rate than expected. The Soft Arkansas removed steel roughly 20% faster than the Hard Arkansas and 40% faster than the Black and Translucent stones. The Hard Arkansas removed metal 20% faster than the Black and Translucent. The Black and Translucent removed steel at roughly the same rate.
The Translucent Arkansas has a finer effective grit than the Black Arkansas. The Black Arkansas is an extra fine stone. It was used for over a century by the medical profession and our grandfathers sharpened their straight razors on it but the translucent is finer still.
Related Articles: The Soft Arkansas has typically been stated at anywhere from 400 to 800 grit. The Soft Arkansas stone is close to 1200 grit.
The Hard Arkansas stone grit is slightly finer than we thought at 1500 grit. Previous estimates put it at somewhere between 800 and 1200 grit.
The test results showed us the Black Arkansas grit is 2300 to 2500 which is exactly what we expected. No surprises here.
From practical experience I have always felt the Arkansas Translucent stone is 4000 grit. There are straight razor users who have put it as high as 8000 grit. This test puts Translucent Arkansas equal to 3500-4000 grit.
The Soft Arkansas stone removed metal at a much faster rate than expected. The Soft Arkansas removed steel roughly 20% faster than the Hard Arkansas and 40% faster than the Black and Translucent stones. The Hard Arkansas removed metal 20% faster than the Black and Translucent. The Black and Translucent removed steel at roughly the same rate.
The Translucent Arkansas has a finer effective grit than the Black Arkansas. The Black Arkansas is an extra fine stone. It was used for over a century by the medical profession and our grandfathers sharpened their straight razors on it but the translucent is finer still.
To learn more about Arkansas Stones click here - What is an Arkansas Stone?
For Arkansas Stone Frequently Asked Questions please click here - Arkansas Stones FAQ
To read more articles about sharpening click here - Sharpening Articles
We always welcome feedback about our articles. For feedback, suggestions or comments please Contact Us.For Arkansas Stone Frequently Asked Questions please click here - Arkansas Stones FAQ
To read more articles about sharpening click here - Sharpening Articles
References:
1. Arkansas Geological Survey (formerly Arkansas Geological Commission) - Novaculite (Silica Stone)
2. Arkansas Archaeological Survey - Arkansas Archeological Survey 2016 "Arkansas Novaculite: A Virtual Comparative Collection".
3. ANSI B74.12 : American National Standards Institute; Specification for Size of Abrasive Grain-Grinding Wheels, Polishing and General Industrial Uses.
4. UAMA B74.12-2018: Unified Abrasives Manufacturers' Association, 07/20/2018, Specifications for the Size of Abrasive Grain - Grinding Wheels, Polishing and General Uses.
5. 3M Company - What Does "Grit" Mean?
6. International Gem Society - The History of Lapidary
7. International Gem Society - Gem Cutting Abrasives In Grit, Mesh, and Microns
8. Gesswein Canada - Grit = Micron = Mesh Conversion Chart
9. Holbrook, D. F., and Stone C. G., 1978, Arkansas Novaculite - A silica resource, in Johnson, K. S. and Russell, J. A., eds., Thirteenth Annual Forum on the Geology of Industrial Minerals: Oklahoma Geological Survey Circular 79, p. 51-58. 6. International Gem Society - The History of Lapidary
7. International Gem Society - Gem Cutting Abrasives In Grit, Mesh, and Microns
8. Gesswein Canada - Grit = Micron = Mesh Conversion Chart